Double Layer Roll Forming Machine
Double Layer Roll Forming Machine
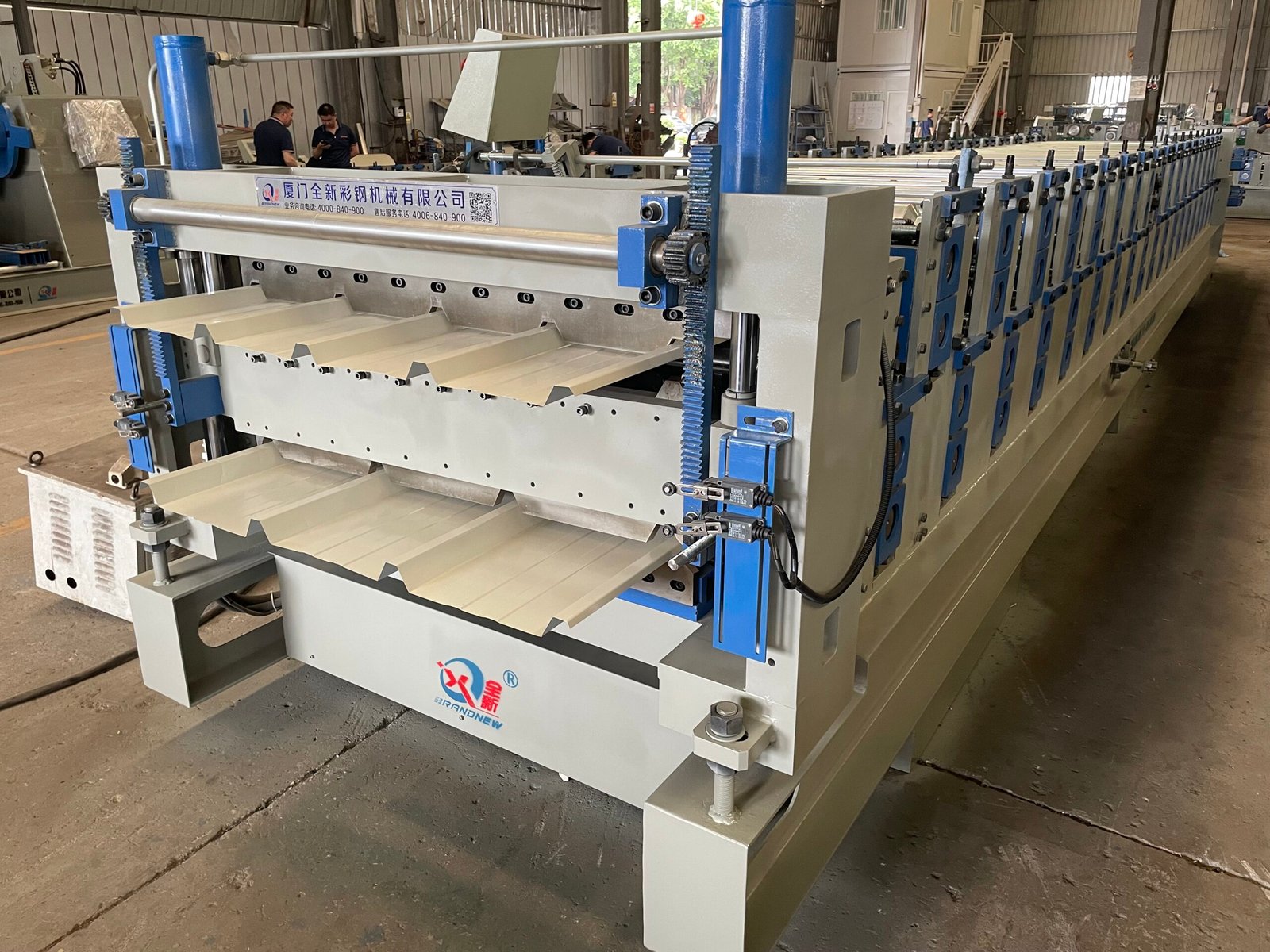
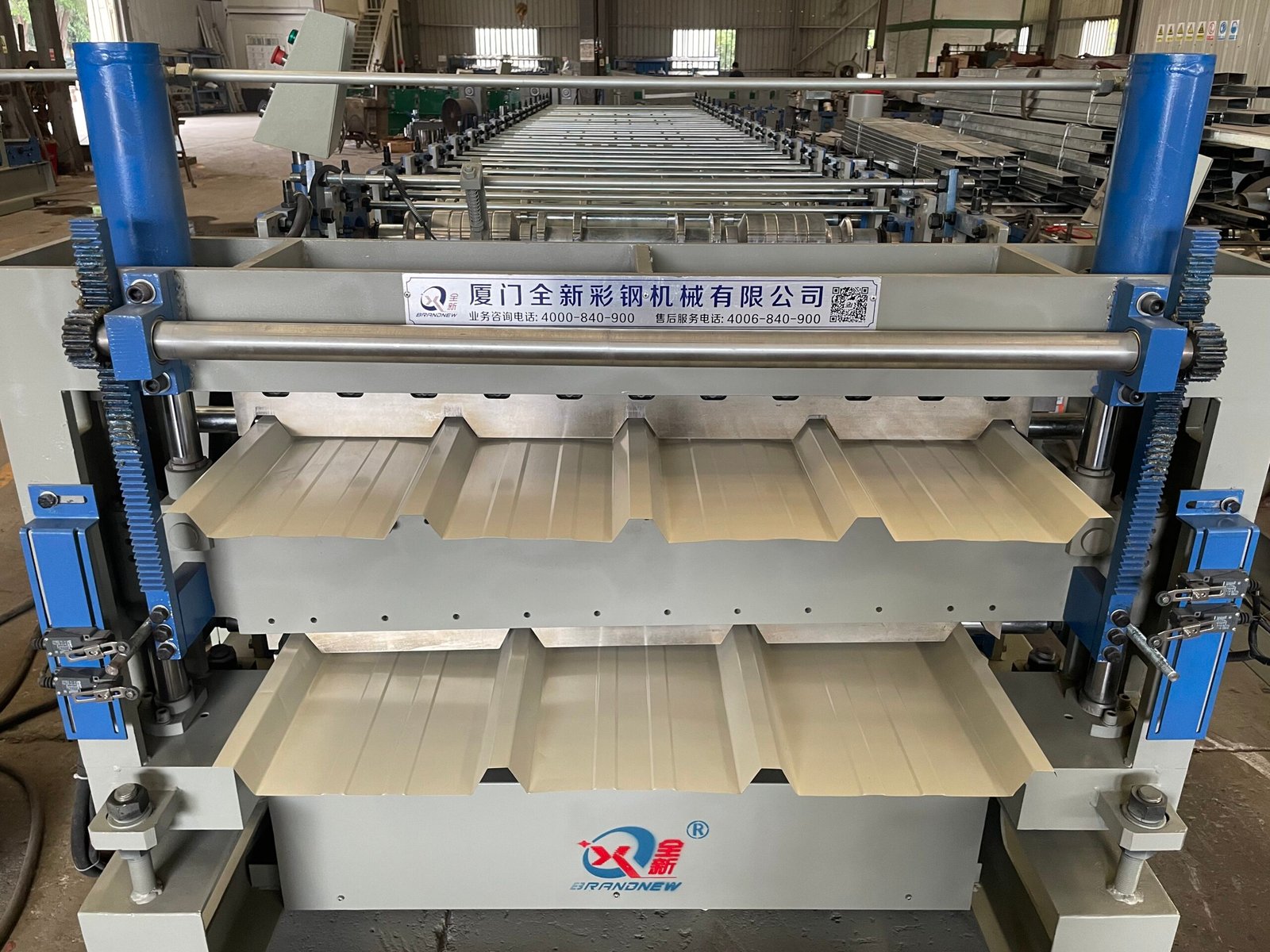
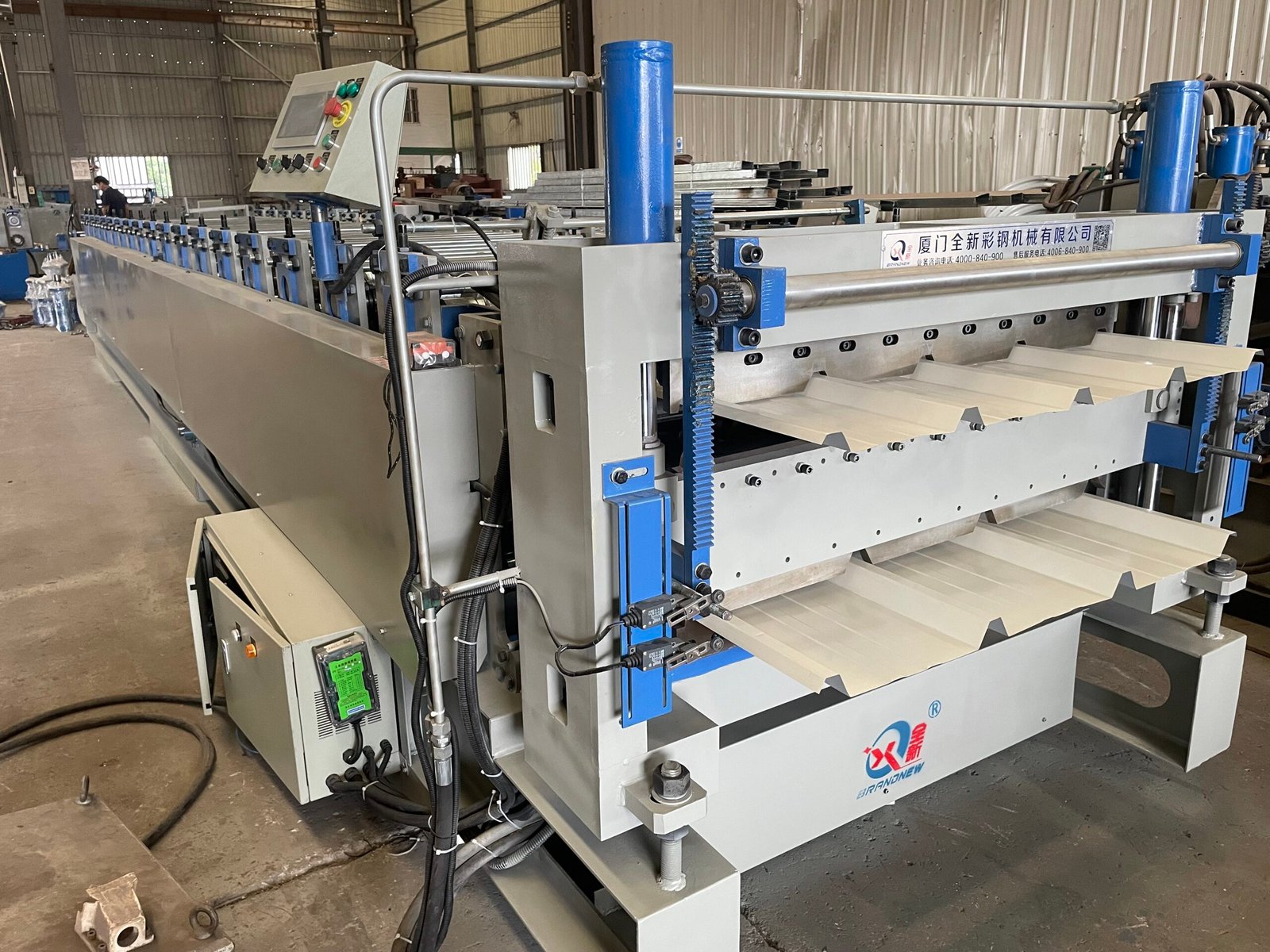
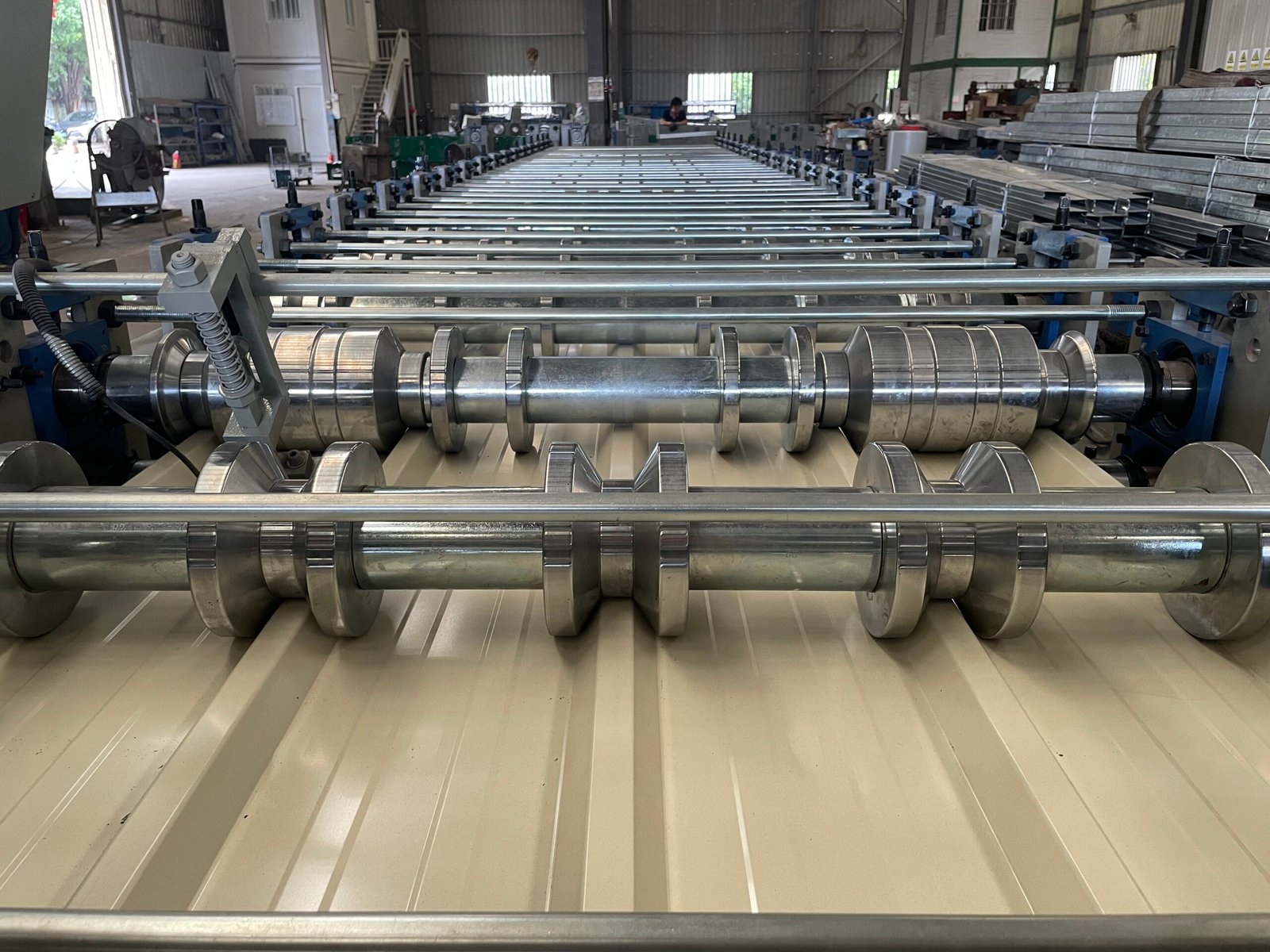
Double Layer Roll Forming Machine
Beenew automatic double layer roll forming machine integrates a decoiler, feeding/leveling device, pre-shear, roll forming system, hydraulic post-cutting, run-out table, hydraulic station, and PLC control system.
Its extended production line ensures precise, high-quality profiles while reducing time and labor, significantly boosting efficiency for modern manufacturing demands. Designed for ease of operation, it guarantees stable performance and consistent precision throughout production.
Flow chart
De-coiler – Leveling device — roll forming parts -Post Cutting system– Stack
Material
Coil Width: 900–1010mm
Thickness: 0.4–0.8mm
Material: PPGI
Yield strength of raw material: 245Mpa
Main Components of Roll Forming Mill
1. Hydraulic decoiler
Segment Opening/Closing Power: Mechanical-driven
Segment Rotation Power: Pulled by forming system
Number of Segments: 4
Segment Expansion Range: 460–520mm
Mandrel Center Height: 0.65m
Feeding Speed: Synchronized with roll forming machine operation
2. Coil guiding device
Features:Ensures smooth, precise material feeding
Components: Steel plate platform, dual pitching rollers, positioning stop block Guides coil alignment and transfers to forming system
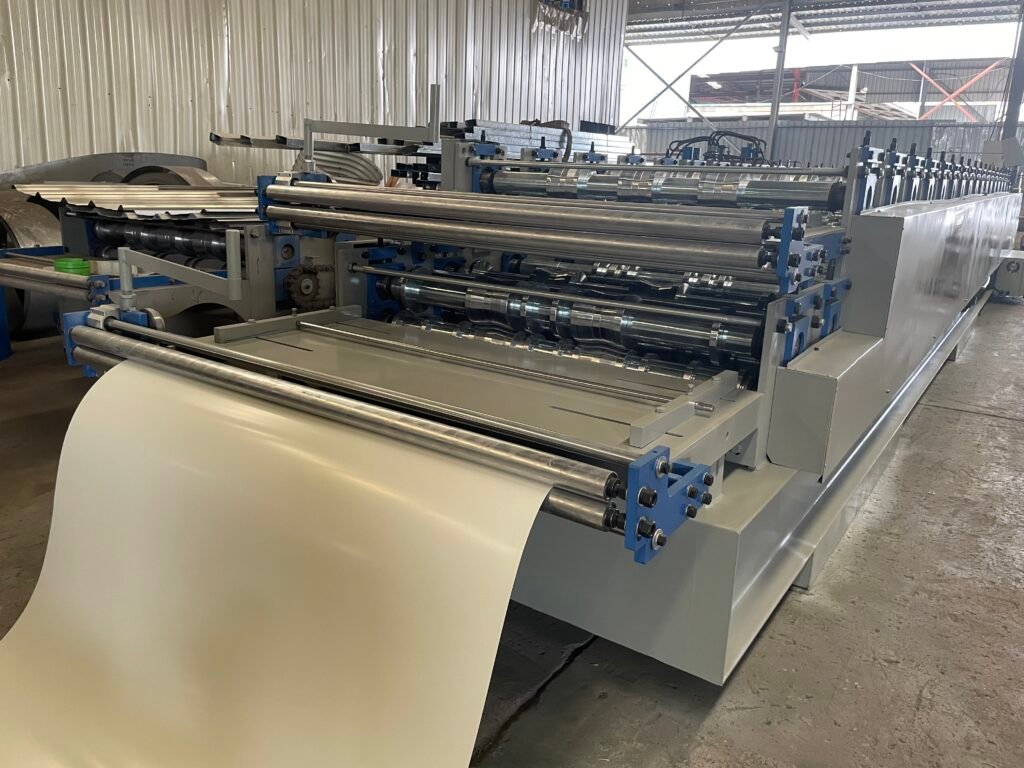
3. Roll Forming Machine
Frame: Modular welded structure; exterior walls screw-assembled post-rotational blasting
Rollers: High-grade No.45 forged steel, CNC-machined; double-ground shafts for precision alignment
Surface Treatment: Hard chrome-plated (0.05mm) post-machining for enhanced durability
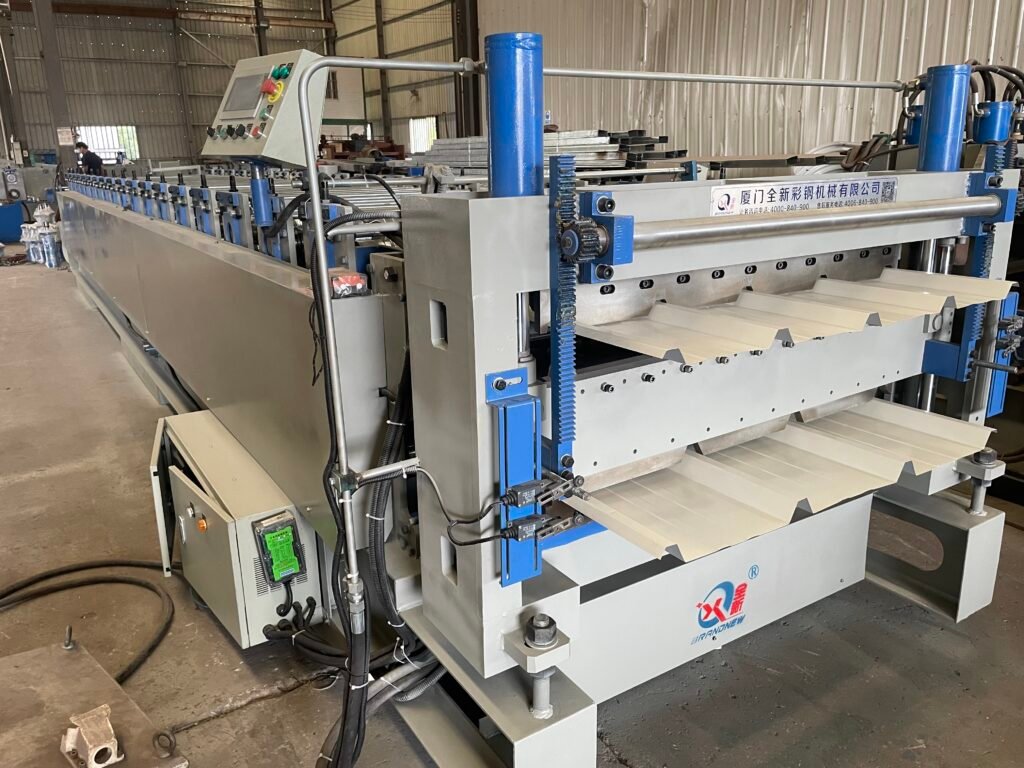
4. Hydraulic Post Cutting
Control & Cutting: PLC-controlled cycle (auto-stop → cut → auto-restart)
Power: Hydraulic-driven
Frame: Welded steel construction
Components: Non-contact photoelectric stroke switch; automatic length measurement
Process: Post-forming cutting to specified lengths
5. Hydraulic station:
Control: Gear pump-driven; activates cutter after oil fills reservoir
Components: Hydraulic reservoir, pump, 2 pipes, 2 solenoid valves
Quality: Premium-brand hydraulic components ensure stability, leak resistance, and longevity
Power Supply: Closed oil tank delivers initial cutting force; auto-off during idle to conserve energy
5. Product track
Unpowered, 3 units in total, equipped with rollers on the top for easy movement
After-Sales Service for Double Layer Roll Forming Machine
1)Warranty Coverage
A comprehensive 2 years warranty is provided, complemented by lifetime technical support.
2)Delivery Commitment
Machines are delivered within 25-40 working days after confirming receipt of the deposit payment.
3)Service Guarantee
24 months free maintenance service for all components.
Lifetime paid service available post-warranty, ensuring ongoing assistance for repairs, parts replacement, and troubleshooting.
4)Installation & Training Support
On-site installation guidance and in-person training are offered if clients visit our factory for machine inspection.
Our engineers will train your technicians/workers in machine operation, maintenance, and safety protocols.
FAQ
Q: Are you a trading company or a manufacturer?
A: We are a direct manufacturer with a dedicated production team and export-focused service expertise in cold roll forming machinery.
Q: Can the machine produce only one panel profile?
A: No. Our machines are engineered for multi-profile versatility, supporting wider and dual-layer production capabilities. A single unit can produce 3+ distinct panel profiles with tooling adjustments.
Q: What is the typical lead time for machine production?
A: Standard lead time is 20–45 business days. For urgent orders, we prioritize production to expedite delivery without compromising quality.
Q: How is quality control ensured during manufacturing?
A: Our rigorous QC protocol includes raw material inspection,precision machining of rolls and critical components.
Assembly verification,surface and shaft integrity testing,pre-shipment operational trials and packaging checks.
Q: What if the machine malfunctions?
A:24-month warranty,Free replacement of irreparable parts (customer covers shipping fees).
Post-warranty support: Lifetime technical assistance and negotiated repair solutions.
Q: What differentiates you from competitors?
A: Our strengths include customer-centric service with tailored engineering solutions.
Low-maintenance, user-friendly designs for quick installation and operation.
Value-added guidance to optimize your ROI and product performance.
Q: Can we partner as your international agent?
A: Absolutely! We actively seek collaborations with distributors or agents to sale our roll forming machine.
No. | Main Parameters | Roll Forming M/C Parameters | ||
1. | Material Thickness | 0.4-0.8mm | Forming Stations | 18-step |
2. | Feeding Width | According to the drawing | Body Frame | H350 |
3. | Application Material | Galvanized sheet/Cold rolled sheet | Side Wall Thickness | 18mm |
4. | Electrical Standard | 380V/50Hz/3Ph | Shaft Diameter | 45# Steel, φ70/65mm |
5. | Manual Decoiler Diameter | 5T-600mm | Main Motor Power | 7.5 KW |
6. | Yield Strength | G235Mpa | Screw Bolts | Grade 8.8 |
7. | Forming Speed | 15m/min | Effective Width | As customer design |
8. | Control System | PLC Control System | Roller | 45#forging steel with chromium plate |
9. | Hydraulic Motor | 5.5KW | Machine Color | Blue+gray(or customized) |
10. | Testing Material | Beenew will supply the dimensions of the feeding material for procurement two weeks prior to the machine testing. |
Related Products
Request A Quote
If you have any questions or require more detailed information about our roll forming solutions, please contact us by clicking on the link below.
Our product specialists will be in touch with you shortly to discuss your requirements!