Door Frame Roll Forming Machine
Door Frame Roll Forming Machine
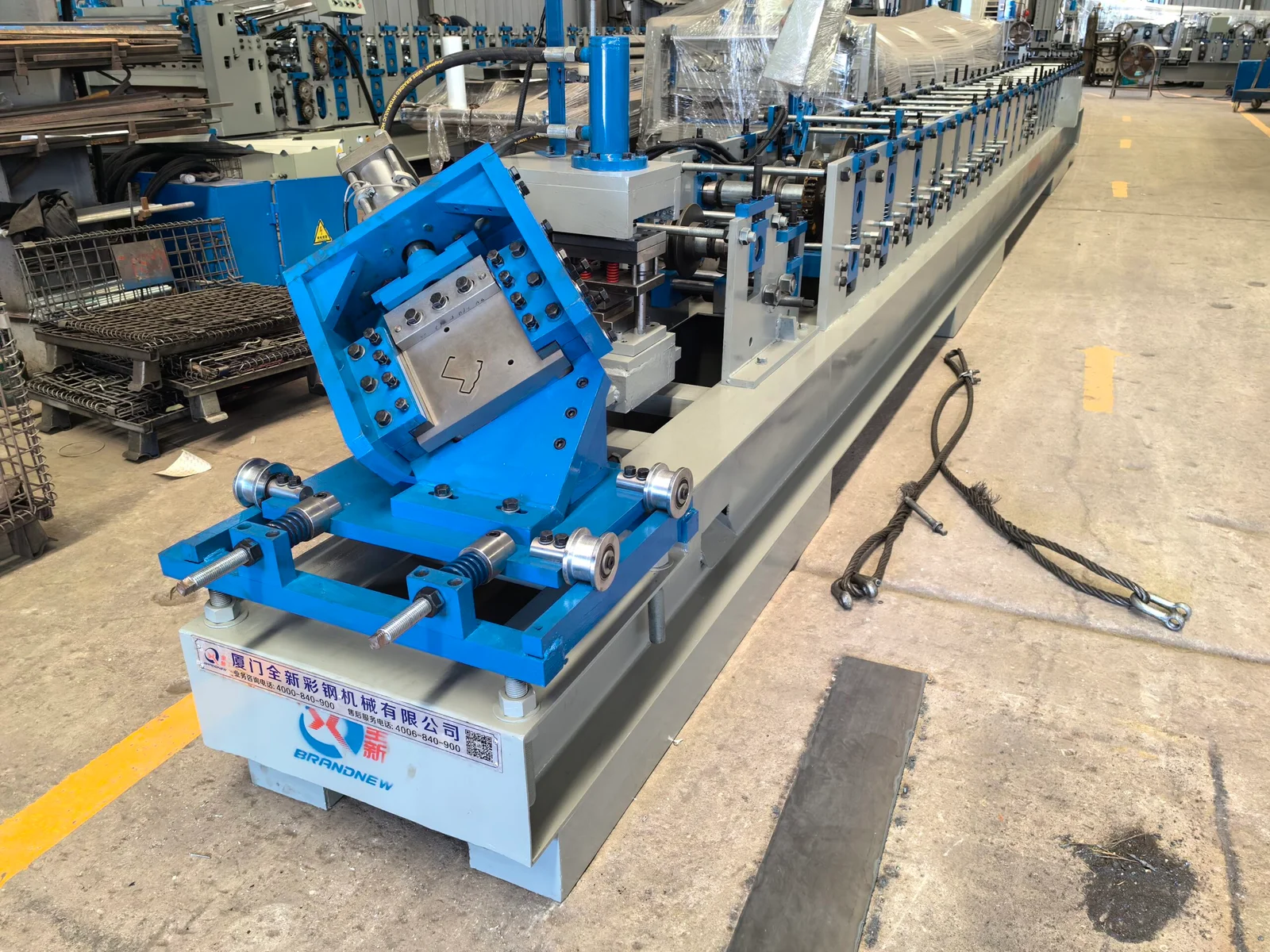
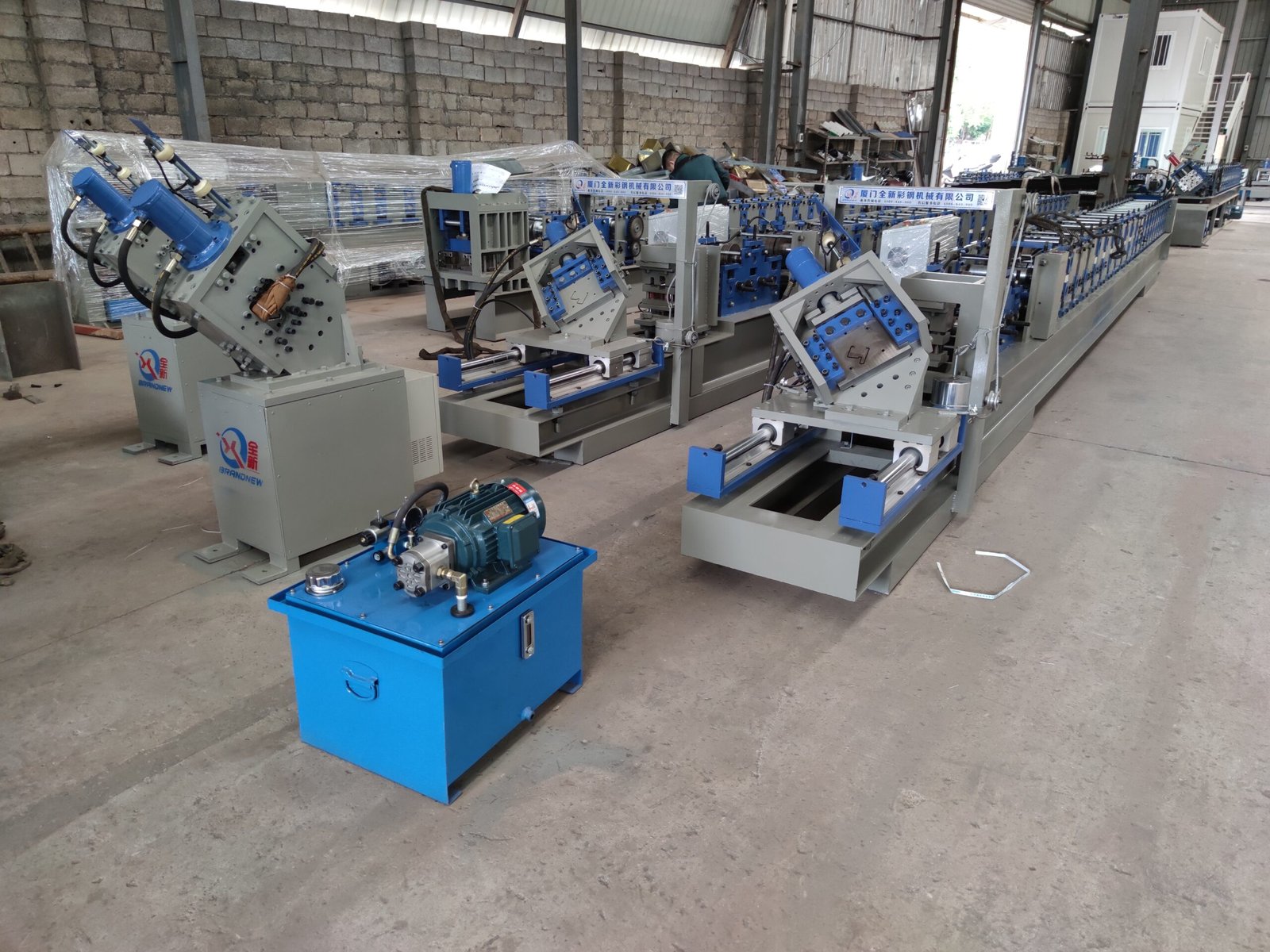
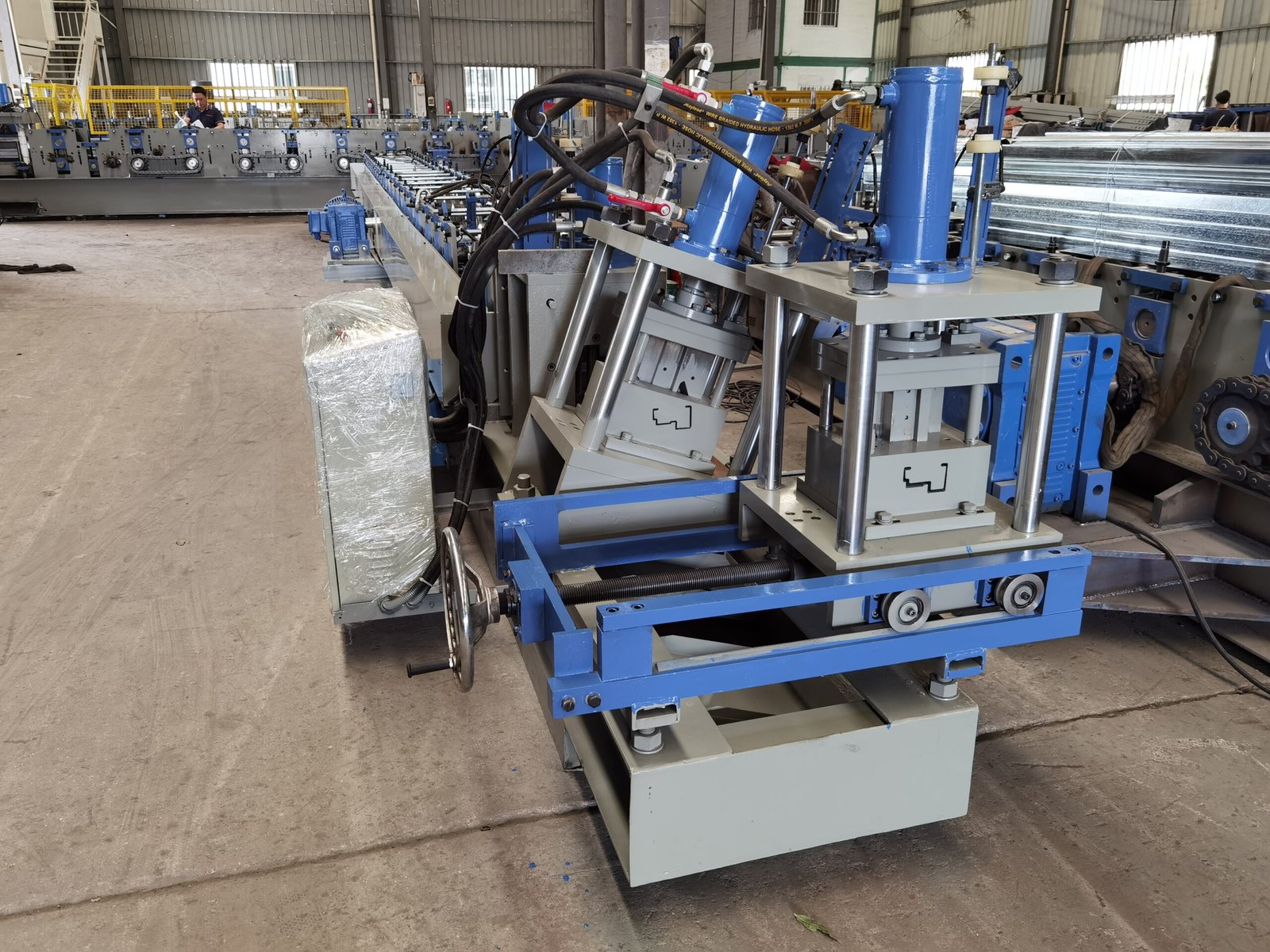
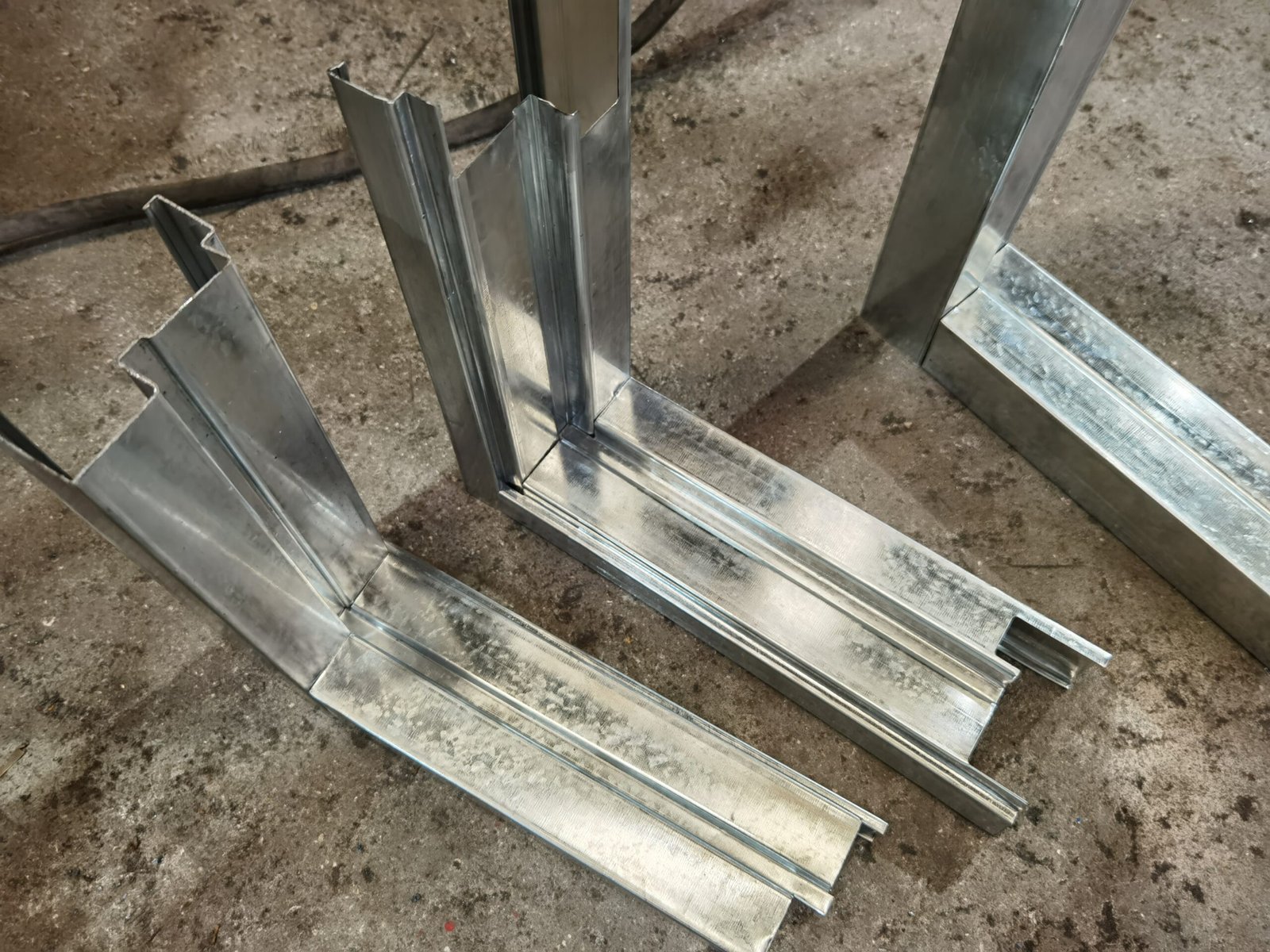
Door Frame Making Machine
The Beenew Door Frame Roll Forming Machine combines a decoiler, feeding/leveling unit, roll forming system, hydraulic post-cutting, run-out table, hydraulic power station, and PLC control.
Its extended production line ensures high-quality profiles with minimal time/labor, boosting efficiency for modern manufacturing needs. Designed for simplicity, it delivers stable operation and precision throughout production.
Flow chart
Decoiler → Sheet guiding → Hydraulic punching system → Roll forming line → Post-Cutting → Product rack

Material
Profile Size Adjustment Type: Roller Sleeve Replacement System
Compatible Coil Thickness: 1.5 mm
Applicable Raw Materials: Galvanized steel sheet; Galvanized color-coated sheet
Raw Material Yield Strength: Q235-grade, 235 MPa
Main Components of Door Frame Making Machine
1.Decoiler
Capacity: 5 tons
Inner diameter: 600mm
2. Pre-Punching System
5 cylinders punching device,1 set
Punching dies,10 sets
Punch and die materials: Cr12 steel with precision finishing and heat treatment
3.Roll Forming Machine
Main Frame Construction: Individually welded frame components with exterior walls screw-connected after rotary shot blasting surface treatment.
Roller Material: High-grade No. 45 forged steel, processed via digitally controlled machining for dimensional accuracy.
Roller Shaft Precision: Precision-ground twice using specialized grinding equipment to guarantee final product dimensional consistency.
Surface Treatment: Hard chrome plating (0.05 mm thickness) applied post-machining via precision tooling, ensuring extended durability of forming rollers.
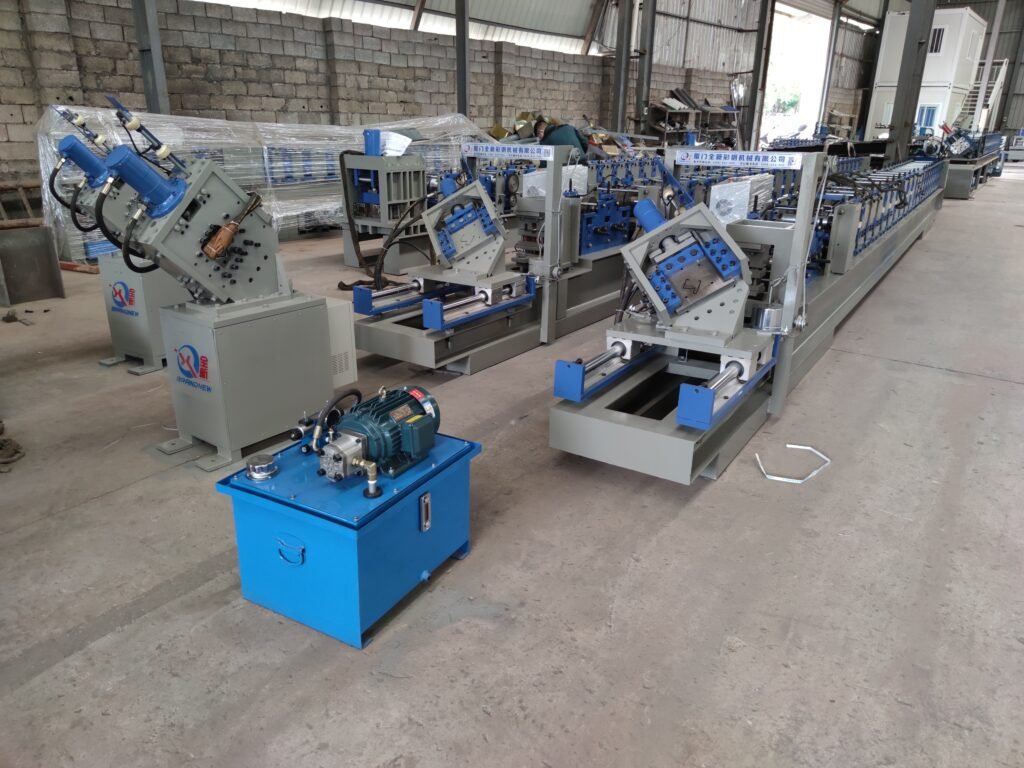
4.Hydraulic Post Cutting Unit
Operation Mode: Stop-cut mechanism with post-cutting execution
Tooling Configuration: Dual-tool setup – dedicated blade sets per product specification
Blade Material: Cr12 tool steel, quenched and hardened to HRC 60-62.
Frame Design: Welded structural frame for enhanced rigidity and vibration resistance
Cutting Precision:Heat-treated cutting frame to minimize product deformation
Cutting length tolerance: ±1 mm.
Power Source: Hydraulically driven via dedicated hydraulic power station
Automation:PLC-programmed length control with rotary encoder for real-time measurement
Automated stop-cut operation: Triggers cutting upon reaching preset length, resumes continuous operation post-cut
5.Hydraulic Power Unit
Function: Delivers hydraulic power to operate the cutting mechanism
Power Output: 7.5 kW electric motor (standard: 380V/50Hz or as per regional requirements)
6. Product Rack
Used to Collect the final product,convenient to be stacked
Support length: 1 set(3 meters)
7. Product Sample
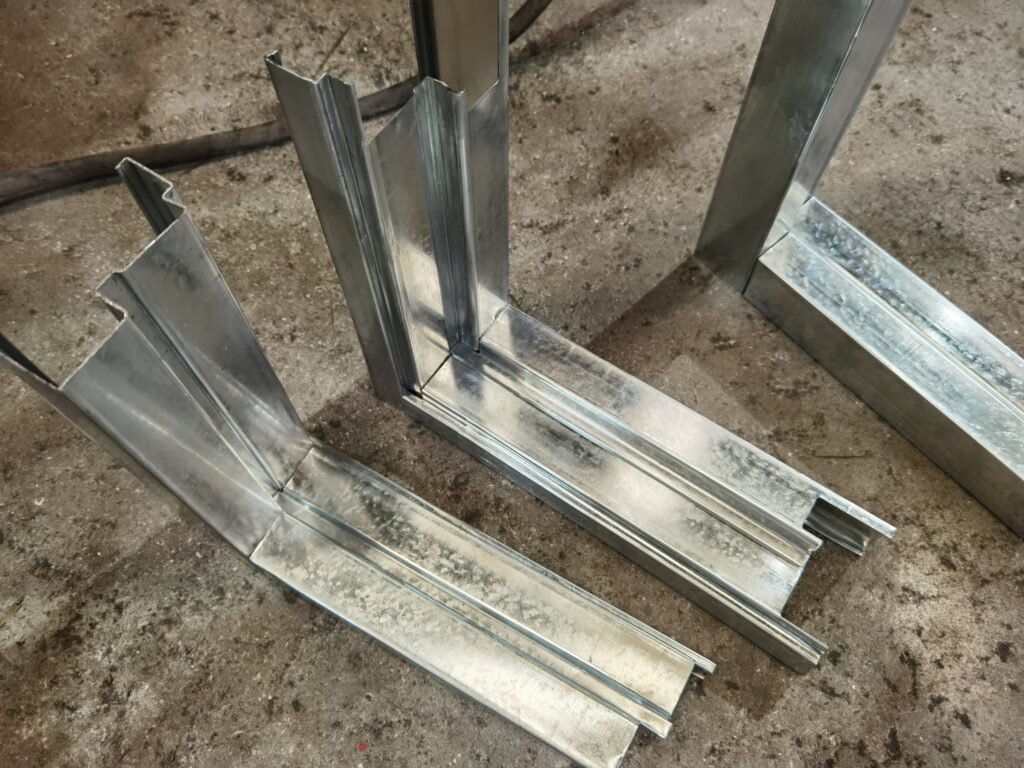
FAQ
Q: Are you a trading company or a manufacturer?
A: We are a direct manufacturer with a dedicated production team and export-focused service expertise in cold roll forming machinery.
Q: Can the machine produce only one panel profile?
A: No. Our machines are engineered for multi-profile versatility, supporting wider and dual-layer production capabilities. A single unit can produce 3+ distinct panel profiles with tooling adjustments.
Q: What is the typical lead time for machine production?
A: Standard lead time is 20–45 business days. For urgent orders, we prioritize production to expedite delivery without compromising quality.
Q: How is quality control ensured during manufacturing?
A: Our rigorous QC protocol includes raw material inspection,precision machining of rolls and critical components.
Assembly verification,surface and shaft integrity testing,pre-shipment operational trials and packaging checks.
Q: What if the machine malfunctions?
A:24-month warranty,Free replacement of irreparable parts (customer covers shipping fees).
Post-warranty support: Lifetime technical assistance and negotiated repair solutions.
Q: What differentiates you from competitors?
A: Our strengths include customer-centric service with tailored engineering solutions.
Low-maintenance, user-friendly designs for quick installation and operation.
Value-added guidance to optimize your ROI and product performance.
Q: Can we partner as your international agent?
A: Absolutely! We actively seek collaborations with distributors or agents to sale our roll forming machine.
No. | Main Parameters | Roll Forming M/C Parameters | ||
1. | Material Thickness | 1.5mm | Forming Stations | 18-step |
2. | Feeding Width | According to the drawing | Body Frame | H350 |
3. | Application Material | PPGI | Side Wall Thickness | 18mm |
4. | Electrical Standard | 380V/50Hz/3Ph | Shaft Diameter | 45# Steel, φ75mm |
5. | Manual Decoiler Diameter | 5T-600mm | Main Motor Power | 11.0 KW |
6. | Yield Strength | G235Mpa | Screw Bolts | Grade 8.8 |
7. | Forming Speed | 20-25m/min | Effective Width | As customer design |
8. | Control System | PLC Control System | Roller | 45#forging steel with chromium plate |
9. | Hydraulic Motor | 5.5KW | Machine Color | Blue+gray(or customized) |
10. | Testing Material | Beenew will supply the dimensions of the feeding material for procurement two weeks prior to the machine testing. |
Related Products
Request A Quote
If you have any questions or require more detailed information about our roll forming solutions, please contact us by clicking on the link below.
Our product specialists will be in touch with you shortly to discuss your requirements!